Автоклавный газобетон
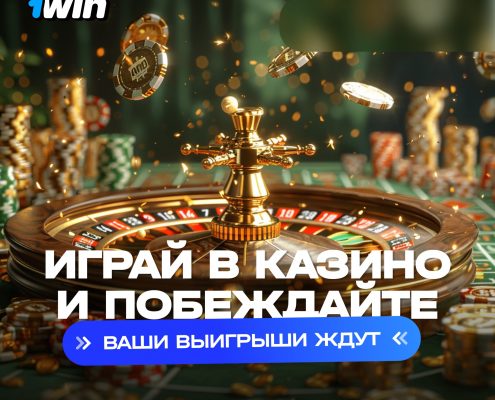
Бетон, имеющий ячеистую структуру, называется газобетоном. Он представляет собой искусственный камень, у которого весь объем пронизан порами. Затвердение, происходящее под давлением с помощью пара в автоклаве, послужило его названию. Давление в автоклаве выше атмосферного и составляет примерно 12 атмосфер, температура обработки изделий – 190 градусов.
Автоклавный бетон получают из цемента, песка, негашеной извести, воды с добавлением немного алюминиевой пудры. В процессе химической реакции извести и алюминиевой пудры при вспенивании смеси образуются поры диаметром до 3-ех мм, заполненные воздухом.
Постройка, выполненная из такого материала, получила название «Каменное дерево» за совмещение свойств дерева и камня.
Свойства автоклавного газобетона
- легкая механическая обработка;
- экологичный;
- сочетание прочности камня и веса дерева;
- высокая теплоизоляция (коэффициент теплопроводности – 0,12 Вт/м°C);
- пожаропрочный;
- высокая степень шумопоглощения;
- устойчивый к воздействию неблагоприятных условий внешней среды;
- водо- и паронепроницаем;
- долговечный. Соблюдение технологии изготовления и строительства позволяет эксплуатировать постройки до100 лет;
- не гниет.
Технология изготовления автоклавного газобетона
- Подготовка смеси. Все составляющие материалы в заданных пропорциях в автоматическом режиме смешиваются до получения состава имеющего консистенцию не густой сметаны.
- Заливка в формы, получение нужного размера блоков. При периодических ударных нагрузках выполняется наполовину объема формы заливка подготовленной смеси. Периодическая вибрация улучшает пористость материала. Взаимодействие алюминия и извести вызывает выделение свободного водорода, подымающего смесь, которая заполняет объем формы полностью. Температура достигает 80 градусов, что приводит к схватыванию цемента. В результате образуются в форме сферы ячейки, заполненные воздухом с порами до трех миллиметров в диаметре. Для качественного получения автоклавного бетона необходимо строго соблюдать технологический процесс изготовления.
- Затвердение массы. Примерно 60-120 минут необходимо для предварительного затвердения массива, при котором он будет достаточно прочным и хорошо резаться.
- Резка массива на готовые блоки. Хорошо затвердевшая масса, но остающаяся достаточно мягкой после распалубки сборной формы, подвергается порезке тонкими струнами на блоки, специальным инструментом формируют пазы и гребни, выполняют карманы для удобства в работе.
- Пропаривание блоков в автоклаве. Готовые изделия помещают в автоклав. В нем происходит термовлажная обработка примерно 12 часов. Температура – 190 градусов, давление пара – 12 атмосфер. В этих условиях материал приобретает достаточную прочность. Специальная установка позволяет получить блоки из автоклавного бетона нужного размера.
- Упаковка. Готовые изделия укладываются на поддоны и передаются на склад готовой продукции или поступают на строительную площадку.
Ответить
Хотите присоединиться к обсуждению?Не стесняйтесь вносить свой вклад!